When we last left off, I had completed a basic outside loop of track. The geometry is a little iffy, so I hope it all works well. It’s a little hard to tell. It would have been much easier to do using flex track, but given my past history of flex track, I really didn’t want to mess with it. Not to mention I can’t GET any without waiting at least a week or driving 200 miles.
In any case, once I had this basic loop, I made a paper template (1:1 scale) of the track and divided it into four basic sections. I took these four templates and laid them out on the spare pieces of 1” thick foam that I had, and traced around them with a sharpie. I placed the foam on a cardboard table, and then took a heavy sharp kitchen knife and cut out the lines. It wasn’t necessary to cut all the way through the foam—just to cut most of the way. Once the lines were cut, I was able to carefully snap the pieces off, just like using the “score and snap” method of cutting styrene.
Side note: I later found that putting my index finger on the top edge of the knife had bored a hole in my skin. Nothing major, but I will certainly cover the knife with a thick towel or something beforehand the next time I cut the foam.
I now laid the foam pieces out in the general shape of the track plan, and attached them to the bottom sheet of foam with Liquid Nails. Once again, thank you Norton Anthologies for finally pulling your weight!
If you’ve never built a layout before, you may be asking, “why elevate the track with another layer of foam?”
Take a look outside. Unless you’re one of the poor souls that live in Lubbock, chances are you can see some chances of elevation in the lay of the land. The “1:1” world is not built on top of plywood. There’s rolling hills, dips and valleys, gorges, mountains, waterfalls, and all kinds of things. In fact, the world is pretty damn bumpy.
Elevating the track up another level makes it much easier to model all these geographic features. Combined with being able to cut out the foam, it’s much easier than trying to build up everything from plywood. This is the first time I’ve actually built a layout like this, so time will tell how it goes.
I let the new pieces of foam dry with the weights on them for a good three days. Two would have probably sufficed, but I had company so I wasn’t able to do anything. The next step was to once again lay out all the track and ensure that it fit. It’s a good thing that I made myself a detailed track plan so there was no doubt as to which pieces went where!
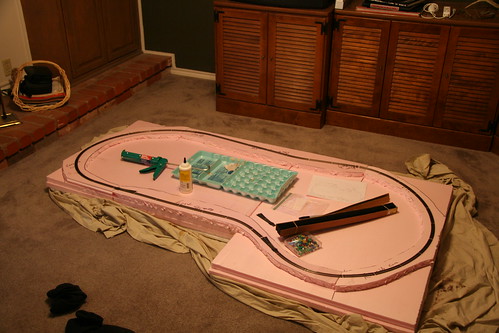
After this track had been laid out and I was reasonably happy with how it looked, I took a sharpie and drew out the plan onto the foam. Working a section at a time, I glued down Woodland Scenics Foam Roadbed. Now, the traditional roadbed material is cork, but I used the foam stuff on my last layout and I really like working with it. It’s very easy to cut, and much easier to curve than cork is. Not to mention cheaper.
The roadbed was held in place with some cheap push-pins that I got at office depot. By the way, I used my 8 year old bottle of foam tack glue, and it still works great. Good stuff. I let the roadbed dry for a few more days. It had to conform to some tight curves, so I wanted to be sure it would stay in the correct spot.

In retrospect, I went about this all wrong. I have several spots where the roadbed simply doesn’t conform to the final position of the track, even though I test-laid the track as I was gluing the roadbed. Next time, I’ll probably lay everything all at once.
While the roadbed was drying, I decided to break out the soldering iron and solder some track together. It’s pretty much the only way to ensure a good electrical connection. I’ve gotten a little better at soldering over the years, but I’m still very much a novice. But I’ve discovered the one great secret to soldering rails: Rosin Paste. The paste is a gooey, yellow substance that helps the solder flow where you want it. It only takes a tiny amount, so a toothpick is the perfect applicator. After that, I simply hold the soldering iron to the railjoiner for a few seconds, and the solder flows freely. Much easier than I thought it would be. I can’t even imagine soldering without the paste now.
I decided to only solder the straight sections, as I was worried about soldering the curves and then having them not join up right. So with the roadbed down, I decided I might as well go ahead and glue down the track. Once again, I spread out the foam tack glue, then held the track in place with pins. I also took great care to let the turnouts “float” (in other words, they are NOT glued down). To my surprise/relief, everything seems to fit well, and two days later I took out the pins and rolled some cars around. It seems very smooth at this point, but rolling some cars around can’t match actually pulling a train.
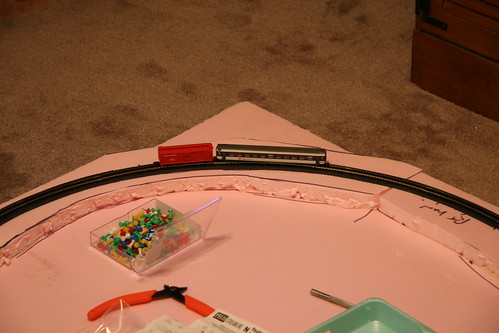
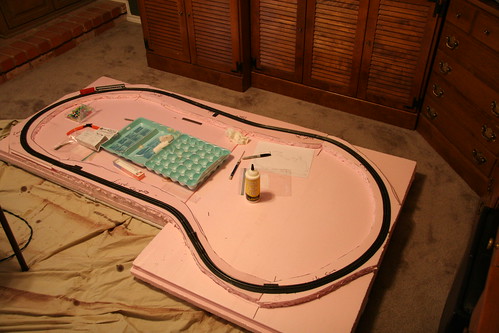
Next: it’s time to get some power to the rails. Wiring can be fun! (It can’t be fun.)
Also, in case you haven't figured out, all the photos (and more photos) are on Flickr:
http://www.flickr.com/photos/cameron_talley/sets/72157616587278989/
No comments:
Post a Comment